Compressed air dryer is as important to keep your air system running at peak efficiency
GSA’s compressed air dryer is highly reliable and efficient in use
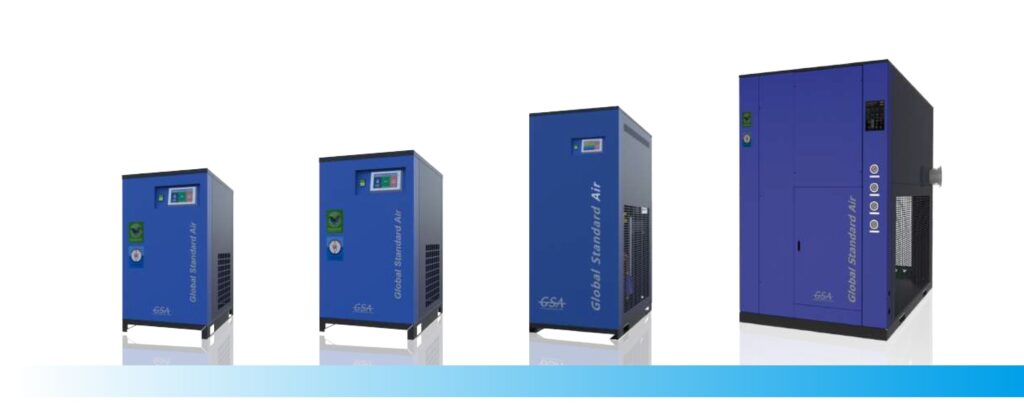
Reduction of Energy Consumption
Generation-III, Energy-saving Refrigerated Air Dryer
GSA’s cycling refrigerated air dryer is a latest energy-saving model which stores cooling energy, using phase change materials (PCMs) accumulated in a specially designed heat exchanger. It cools and freezes PCMs, using reserve cooling energy generated under no/low load and chills compressed air with accumulated latent heat. It reduces operating costs by stopping operation while such latent heat is burnt out and PCM temperature rises for a certain period of time.
Using a patented heat exchanger, the cycling refrigerated air dryer is able to store a huge amount of cooling energy, which cannot be done in regular refrigerated dryers. It can save energy in an innovative fashion. The heat exchanger of a standard refrigerated air dryer is comprised of an air-air heat exchanger and an air-refrigerant heat exchanger. However, the generation-III, cycling refrigerated dryer consists of three different parts: i) air-air heat exchanger, ii) air-PCM heat exchanger, iii) refrigerant-PCM heat exchanger. The above three heat exchangers in a PCM heat exchanger are connected to each other systematically. Made with the same material, they generate the best efficiency and performances. In addition, the cycling refrigerated air dryer has such high latent heat that it maximizes energy-saving efficiency, using high-purity alkane PCMs with which a large amount of cooling energy can be saved. With a refrigerant pressure transmitter, furthermore, it features various latest technologies and systems, optimizes the cooling system and enhances cooling efficiency, energy utility and user convenience.
Accumulated Heat Amount
Heat Exchanger | Material | Specific Heat (J/kg) | Thermal Conductivity (kcal/mh℃) |
PCM Latent Heat (J/kg) |
Quantity of Heat (1kg x △10℃) |
Heat Storage Ratio |
---|---|---|---|---|---|---|
Shell & Tube | Copper | 389 | 332 | N/A | 3890 | 100% |
Plate heat exchanger | Stainless | 464 | 14 | N/A | 4640 | 120% |
Aluminum Block | Aluminum | 896 | 196 | 240000 | 8960 | 3300% |
Energy Saving
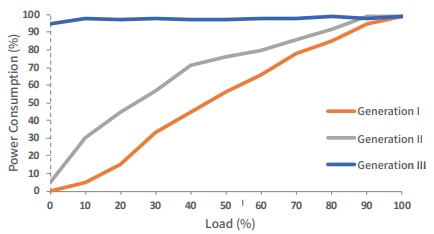
Energy-saving rates when both low-load and no-load conditions are considered
Highly Reliable Generation-III Energy-saving Dryer developed with the Latest Technologies
Generation-III Refrigerated Air Dryer with the Latest Innovative Technologies
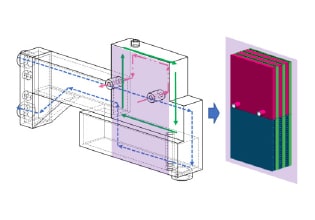
High-efficiency Aluminum PCM Heat Exchanger
The patented GSA PCM heat exchanger is specially designed for efficient heat exchanging with compressed air, refrigerant and PCMs. With great cooling performances and efficiency, it reduces energy consumption innovatively. The high-efficiency aluminum heat exchanger has a larger heat-exchange area and greater performances than other types of heat exchangers such as shell & tube and plate ones. The internally accumulated high-purity PCMs reveal great cooling performances with high latent heat and offer stable dew points with good energy-saving efficiency. Made with the same material, in addition, the GSA air dryer has no thermal resistance and is free from heat exchanger freeze-up or corrosion.

Highly Reliable Drain without Compressed Air Loss
As a separation space with thermister inside the heat exchanger, it shows great condensate separation efficiency. The isolated condensate is discharged through the magnetic float-mounted auto drain. A zero-loss drain adopting either a magnetic float or level sensor depending on a product ensures great operating performances and minimizes performance drop or failure in the drain caused by oil, dirt and various contaminants.

Minimization of Compressed Air Loss with Low Differential Pressure
We minimized differential pressure with a large heat-exchange area and sufficient cross section for the passage of compressed air. We enhanced heat-exchange efficiency and reduced differential pressure by minimizing resistance, making it possible to operate the compressed air system more efficiently at lower costs.
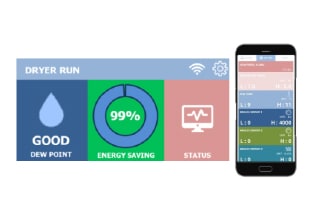
Smart Controller with Diverse Latest Technologies
A multifunctional controller featuring a 4.3” TFT color touch panel offers an intuitive interface through which users are able to check current operations and energy-saving status easily. In addition, if mobile communication features are added, it is possible to check current operations and diverse information and features through WIFI and BT. Users are also able to check the system near the system or in the distance through an Android app, using an intranet.
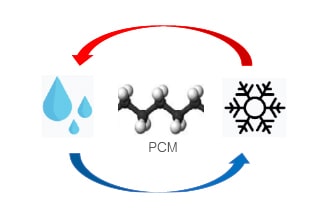
Maximization of Energy-saving Effects through High-purity/High-efficiency PCMs
The PCM refrigerated dryer maximized energy efficiency, using high-purity alkane PCMs. Compared to others, the high-purity alkane PCMs are able to store more energy with high latent heat. In addition, they are durable and have a stable phase change cycle. In addition, they maximize the super cooling- and corrosion-free properties of an aluminum heat exchanger and ensure stable operation and performances.
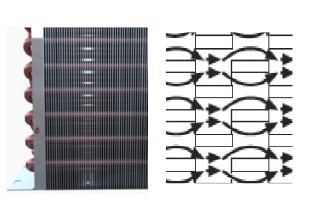
Efficiency Maximization with High-efficiency Condenser
For stable performances even under unfavorable circumstances such as high temperature, grooved cooper tube and corrugated split fin were applied. Since they are expanded in a complete and uniform manner, fin adhesion is high, applying condensate with a high coefficient of heat transfer. Therefore, it guarantees stable operations under diverse environments including hot temperature.
Technical Specification
Design Conditions
- Inlet Pressure : 7 barg
- Inlet Temperature : 38℃
- Pressure Dew Point: : 2 ~ 10℃
- Design Pressure : 14 barg
- Design Temperature : 70℃
- Ambient Temperature : 32℃
References
- All models use either R-134a or R-22 refrigerant. Other models adopting different types of refrigerants are also available.
- The flow rate is based on 60Hz.
- Other electrical specifications are also available.
- A unit with 15barg or higher operating pressure is customizable.
- Large models bigger than those stated in the specifications are also customizable.
- The specifications are subject to changes without notice for product improvement.

Model | Connection | Air Compressor | Flow Rate | Minimum Electrical Energy | Power Supply | Dimensions | Weight | |||
---|---|---|---|---|---|---|---|---|---|---|
A | HP | N㎥/min | kW | V / Ph / Hz | A | B | C | kg | ||
H Y D |
30N3 | PT 25A | 30 | 3.9 | 0.45 | 220 / 1 / 50, 60 |
360 | 700 | 950 | 70 |
50N3 | PT 40A | 50 | 6.7 | 0.7 | 410 | 710 | 1050 | 100 | ||
100N3 | PT 50A | 100 | 14.2 | 1.17 | 380 / 3 / 50,60 |
460 | 900 | 1250 | 140 | |
150N3 | PT 65A | 150 | 21 | 1.45 | 570 | 1050 | 1400 | 180 | ||
200N3 | FLG. 80A | 200 | 30 | 2.09 | 750 | 1250 | 1460 | 260 | ||
300N3 | FLG. 100A | 300 | 47 | 2.3 | 850 | 1350 | 1650 | 290 | ||
400N3 | FLG. 100A | 400 | 56 | 4.85 | 1200 | 1500 | 1750 | 680 | ||
500N3 | FLG. 150A | 500 | 66 | 6.52 | 1800 | 1750 | 1850 | 980 | ||
600N3 | FLG. 150A | 600 | 85 | 7.72 | 1800 | 1750 | 1850 | 1120 |
Correction Factors
Correction Factor by Inlet Air Temperature | ||||||||||||
---|---|---|---|---|---|---|---|---|---|---|---|---|
Inlet Air Temperature (℃) | 28 | 33 | 38 | 43 | 48 | 53 | 58 | 63 | 68 | 70 | N/A | N/A |
Correction Factor | 1.46 | 1.20 | 1.00 | 0.85 | 0.73 | 0.63 | 0.55 | 0.48 | 0.42 | 0.40 | N/A | N/A |
Correction Factor by Inlet Air Pressure | ||||||||||||
Inlet Air Pressure (barg) | 4 | 5 | 6 | 7 | 8 | 9 | 10 | 11 | 12 | 13 | 14 | 15 |
Correction Factor | 0.84 | 0.90 | 0.95 | 1.00 | 1.03 | 1.06 | 1.09 | 1.11 | 1.13 | 1.15 | 1.17 | 1.18 |
Correction Factor by Ambient Temperature (Air-cooled Models) | ||||||||||||
Ambient Temperature (℃) | 27 | 32 | 37 | 40 | 45 | 50 | N/A | N/A | N/A | N/A | N/A | N/A |
Correction Factor | 1.05 | 1.00 | 0.92 | 0.82 | 0.76 | 0.69 | N/A | N/A | N/A | N/A | N/A |

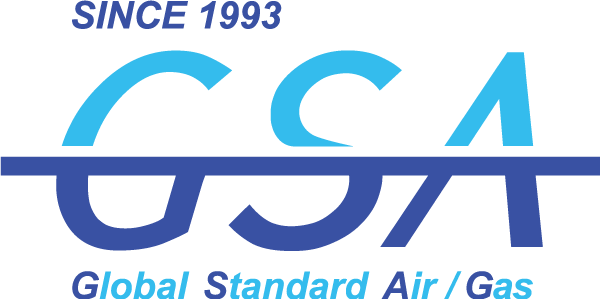
Refrigerated Air Dryers
- +82 31-798-0171~3
- FAX : +82 31-798-0175