Compressed air dryer is as important to keep your air system running at peak efficiency
GSA’s compressed air dryer is highly reliable and efficient in use

Low-temperature Chilling Technology for Compressed Air & Gas
Compressed Air & Gas Chiller
GSA manufactures and distributes a wide variety of products which can help its clients enhance their productivity and product quality.
The Air and Gas Chiller is a product specially designed to meet such client needs. It has been widely used in various fields such as temperature-sensitive manufacturing sectors, food & drink, medicine, petrochemicals and shipbuilding & maritime.
It is used to cool down high-temperature fluids or maintain outlet temperature at a certain level. Fluids can be used in cooling various gases such as nitrogen and oxygen as well as common compressed air. Depending on a cooling range,the Air & Gas Chiller can be divided
into 2 different categories: In a standard air & gas chiller, 50-60℃ fluids are cooled down to 10-20℃. For this, no particular facilities but a filter are needed. A low-temperature air & gas chiller usually cools down fluids up to below zero temperatures. It needs pre-treatment facilities to dehumidify the fluids. Therefore, it is required to keep dew points of the fluids below cooling temperature. In addition, they should be properly insulated to prevent heat loss from low temperature. In a low-temperature air & gas chiller, fluids can be chilled up to 70℃. It features a relatively complicated system, compared to regular ones.
Compressed Air & Gas Chilling Features and Mechanism
GSA’s air chiller is designed to cool down high-temperature compressed air and gas to wide temperature ranges and meet diverse
client needs. It features a refrigerant circuit and ensures the best performances through various apparatus for temperature and refrigerant control.
The air and gas chiller features various layouts depending on the fluid temperature/pressure, fluid type or cooling temperature. High-temperature fluids are cooled down when heat is exchanged with a refrigerant by a specially designed heat exchanger. It can
check various information in addition to inlet/outlet temperature through a multifunctional controller and operating situations in realtime through an option. The condensate generated during cooling is eliminated through a separate drain system. If necessary to control outlet temperature (option), it is controlled precisely by an expansion or hot-gas control valve. An expansion valve or hot-gas electronic control valve is able to control outlet temperature in a quick and accurate manner through organic mechanism between a step motor which can control pening rates precisely (at least hundred – thousand steps) and a controller.
Usage
Just like many other gas systems including refrigerated and desiccant dryers, AIR & GAS CHILLER is now being used in diverse industries. The Air and Gas Chiller has been widely used in various fields such as temperature-sensitive manufacturing sectors (e.g., glass mold surface cooling, high-temperature metal cooling, etc.), pharmaceuticals, food & drink and medicine.
In low-temperature models, air and gas can be cooled up to -70℃. They are available in chilling various gases.
GSA has manufactured and provided products which meet diverse client needs with the latest technologies which have been accumulated for
a long period of time. The company also offers rational and efficient solutions with diverse energy-saving features.
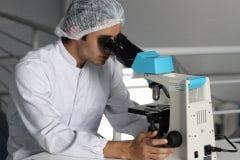
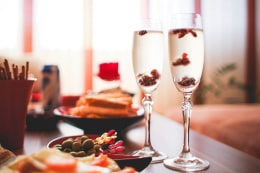

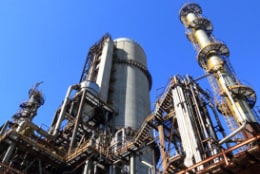


Highly Reliable Compressed Air & Gas Chiller
Product with Diverse Innovative Technologies

High-efficiency Aluminum Heat Exchanger
With a high-efficiency aluminum heat exchanger, GSA refrigerated air dryer offers stable performances with a larger heat-exchange area and greater efficiency than other types of heat exchangers such as shell & tube and plate ones. Made with the same material, the GSA air dryer has no thermal resistance and is free from heat exchanger freeze-up or corrosion.

Highly Reliable Drain without Compressed Air Loss
As a separation space with thermister inside the heat exchanger, it shows great condensate separation efficiency. The isolated condensate is discharged through the magnetic float-mounted auto drain. A zero-loss drain adopting either a magnetic float or level sensor depending on a product ensures great operating performances and minimizes performance drop or failure in the drain caused by oil, dirt and various contaminants.
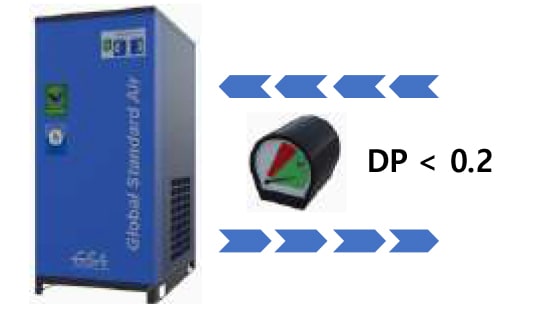
Minimization of Compressed Air Loss with Low Differential Pressure
We minimized differential pressure with a large heat-exchange area and sufficient cross section for the passage of compressed air. We enhanced heat-exchange efficiency and reduced differential pressure by minimizing resistance, making it possible to operate the compressed air system more efficiently at lower costs.
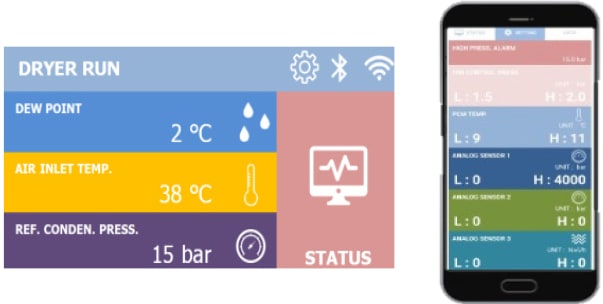
Smart Controller with Diverse Latest Technologies
A multifunctional controller featuring a 4.3” TFT color touch panel offers an intuitive interface through which users are able to check current operations and energy-saving status easily. In addition, if mobile communication features are added, it is possible to check current operations and diverse information and features through WIFI and BT. Users are also able to check the system near the system or in the distance through an Android app, using an intranet.
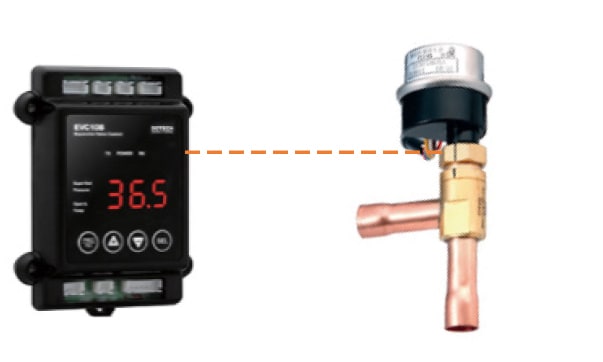
Outlet Temperature Control (Option)
A multifunctional controller featuring PID precision control, an expansion valve having a precision electronic valve which enables precise step control (in 2,000 steps) and a hot-gas bypass valve offers precision control under diverse situations. A high-precision electronic valve is durable and makes little noise. It optimizes a system through auto control and reduces energy consumption.
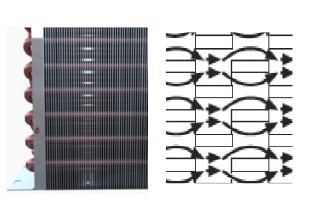
Efficiency Maximization with High-efficiency Condenser
For stable performances even under unfavorable circumstances such as high temperature, grooved cooper tube and corrugated split fin were applied. Since they are expanded in a complete and uniform manner, fin adhesion is high, applying condensate with a high coefficient of heat transfer. Therefore, it guarantees stable operations under diverse environments including hot temperature.
Technical Specification
Design Conditions
- Inlet Pressure: 7 barg
- Inlet Temperature: 32 ℃
- Outlet Temperature: 10 ℃
- Design Pressure: 14 barg
- Design Temperature: 70 ℃
- Ambient Temperature: 32 ℃
References
- It can be used to cool air and gas or for temperature control purposes(Option).
- The flow rate is based on 60Hz.
- Other electrical specifications are also available.
- A unit with 15barg or higher operating pressure is customizable.
- Large models bigger than those stated in the specifications are also customizable.
- The specifications are subject to changes without notice for productimprovement.

Model | Fluid | Connection | Flow Rate | Power Consumption | Power Supply | Dimensions(mm) | Weight | |||
---|---|---|---|---|---|---|---|---|---|---|
A | N㎥/min | kW | V / Ph / Hz | A | B | C | kg | |||
H Y D |
5CH | Compressed Air / Nitrogen / Various gas |
PT 15A | 0.5 | 0.32 | 220 / 1 / 60 | 245 | 555 | 755 | 32 |
7CH | PT 15A | 0.8 | 0.33 | 245 | 555 | 755 | 32 | |||
10CH | PT 15A | 1 | 0.34 | 245 | 555 | 755 | 32 | |||
15CH | PT 25A | 1.5 | 0.5 | 425 | 505 | 710 | 41 | |||
20CH | PT 25A | 2.6 | 0.58 | 425 | 505 | 710 | 41 | |||
30CH | PT 25A | 3.9 | 0.91 | 355 | 655 | 865 | 62 | |||
50CH | PT 40A | 6.7 | 1.39 | 405 | 705 | 955 | 83 | |||
75CH | PT 50A | 10.5 | 2.05 | 455 | 795 | 1045 | 115 | |||
100CH | PT 50A | 14.2 | 2.34 | 380 / 3 / 60 440 / 3 / 60 |
455 | 855 | 1145 | 120 | ||
150CH | PT 65A | 21 | 2.89 | 565 | 1005 | 1330 | 165 | |||
200CH | FLG. 80A | 30 | 4.18 | 550 | 1200 | 1450 | 225 | |||
250CH | FLG. 100A | 39 | 4.4 | 700 | 1200 | 1580 | 240 | |||
300CH | FLG. 100A | 47 | 4.6 | 700 | 1200 | 1580 | 245 | |||
400CH | FLG. 100A | 56 | 9.7 | 900 | 1590 | 1915 | 560 |
Correction Factors
Correction Factor by Inlet Air Temperature (Dry Air) | ||||||||||||
---|---|---|---|---|---|---|---|---|---|---|---|---|
Inlet Air Temperature (℃) | 25 | 32 | 35 | 40 | 45 | 50 | N/A | N/A | N/A | N/A | N/A | |
Correction Factor | 1.15 | 1.00 | 0.85 | 0.7 | 0.6 | 0.5 | N/A | N/A | N/A | N/A | N/A | N/A |
Correction Factor by Inlet Air Pressure | ||||||||||||
Inlet Air Pressure (barg) | 4 | 5 | 6 | 7 | 8 | 9 | 10 | 11 | 12 | 13 | 14 | N/A |
Correction Factor | 0.77 | 0.86 | 0.93 | 1.00 | 1.05 | 1.1 | 1.14 | 1.18 | 1.21 | 1.24 | 1.27 | N/A |
Correction Factor by Ambient Temperature | ||||||||||||
Ambient Temperature (℃) | 27 | 32 | 37 | 40 | 45 | 50 | N/A | N/A | N/A | N/A | N/A | N/A |
Correction Factor | 1.02 | 1.00 | 0.8 | 0.75 | 0.65 | 0.5 | N/A | N/A | N/A | N/A | N/A | N/A |

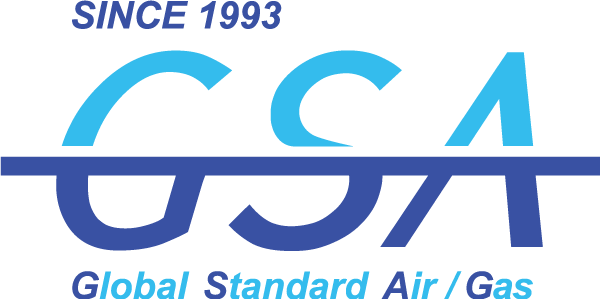
Refrigerated Air Dryers
- +82 31-798-0171~3
- FAX : +82 31-798-0175