PEHB series is used in various fields such as food & beverage, pharmaceuticals, petrochemicals, electronics & semiconductor and medicine
GSA’s desiccant air dryer is able to provide even super-dry compressed air according to user needs
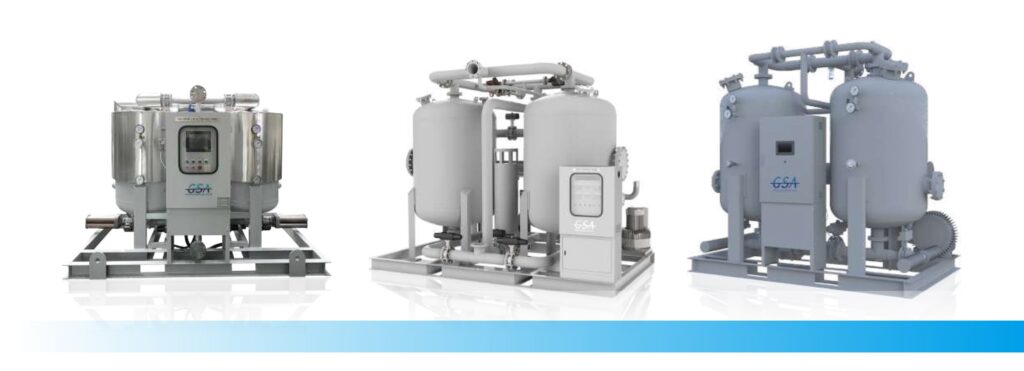
Why Desiccant Air Dryer?
A refrigerated air dryer chills and dehumidifies compressed air, using a refrigerant. To prevent condensate generated while cooling compressed air from being frozen or a heat exchanger from being frozen-burst, dew points are usually kept at 0℃ or higher. For moisture-sensitive processes, therefore, a desiccant air dryer is essential.
In general, a desiccant air dryer offers -40℃ or lower temperature of dew points. It is used in various fields such as food & beverage, pharmaceuticals, petrochemicals, electronics & semiconductor and medicine. In these industries, even a small amount of water might result in process discontinuance or product defect. Therefore, a highly reliable desiccant air dryer is a must-have system.
GSA’s desiccant air dryer is able to provide even super-dry compressed air (-100℃ or below) according to user needs. We have enhanced customer satisfaction through the design of diverse desiccant air dryer systems.
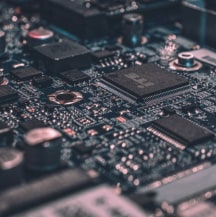
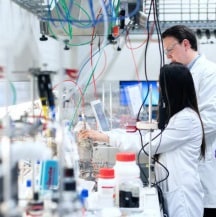
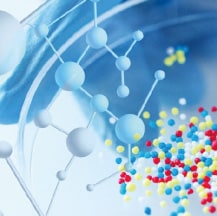
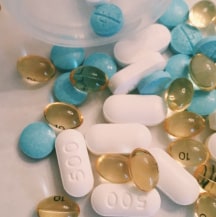
Classification
- A commonly used model with a short process cycle (nearly 10 minutes)
- Simple structure and low power consumption
- About 14% purge consumption
- A model with a long process cycle (8 hours orlonger)
- A heater needed to heat regeneration air mounted
- About 8% purge consumption
- A model with a long process cycle (8 hours orlonger)
- Regenerates a desiccant, using air around the blower and heaterfurnace
- About 3% purge consumption
- A model with a long process cycle (8 hours orlonger)
- Regenerates a desiccant, using air around the blower and heaterfurnace
- Zero purge consumption
Operating Mechanism
Compressed air with high moisture flows into the drying tower. While it moves from the bottom to the top of the tower, moisture is adsorbed by the charged desiccant, producing dry compressed air. While the air is being dried in the drying tower, other towers engage in regeneration process to remove adsorbed moisture. The regeneration process is divided into heating and cooling processes. During the former process, air is sucked in from the outside, using a blower. Then, it is heated through a heater, heating the desiccant in the regeneration
tower. After moisture is removed, it is discharged to the outside through a muffler at the bottom of the regeneration tower. Once the heating process is complete, a cooling process begins. The heated descant is cooled down, using a part of the dry compressed air from the drying tower. Then, it is discharged to the outside through a muffler at the bottom of the regeneration tower. Once the cooling process is completed, the desiccant regeneration process from the regeneration tower is also finished. The purge valve from the regeneration tower is
closed. Then, dynamic pressure process pressurizing regeneration tower starts. Once the dynamic pressure process is done, two towers are transferred. In the drying tower, then, the regeneration process is executed. In the towers where such regeneration process is completed, drying process is executed.
A series of above processes are automatically repeated according to specific time and sequence, producing dry air consecutively. In terms of an operating cycle, it is basically operated for 8 hours. Drying process is executed by two towers (4 hours each). Specifically, itis heated for 2 hours and 30 minutes and cooled for 1 hour and 27 minutes with 3-minute dynamic pressure.
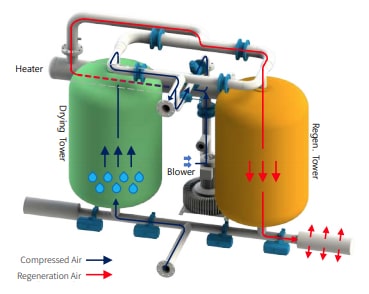
Desiccant Air Dryer for Stable Dew Points
Desiccant Air Dryer with Diverse Features
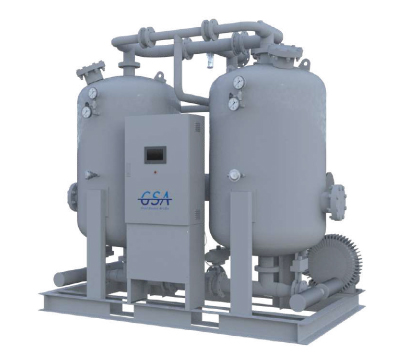


























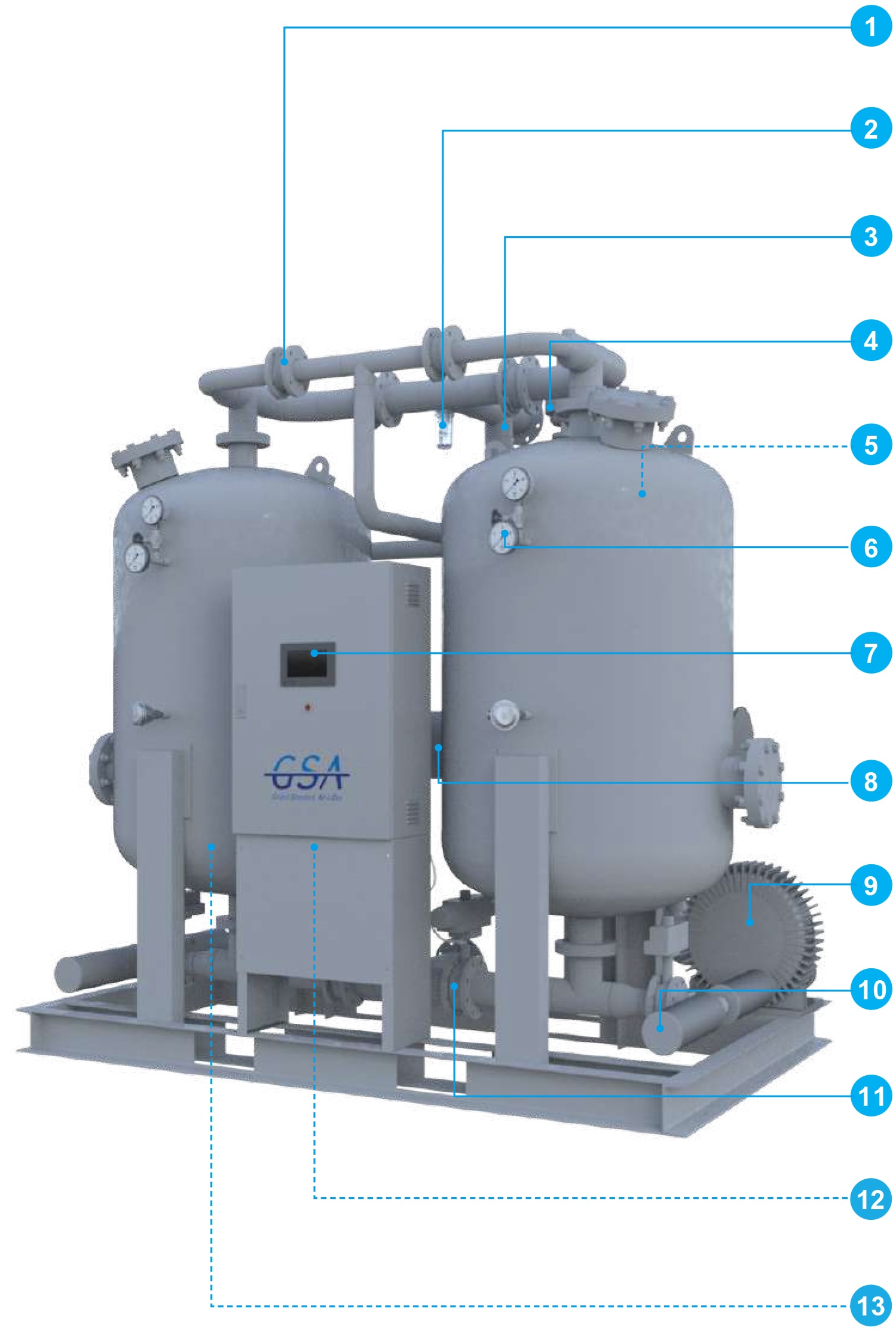
-
PAN/DUAL Check Valve
High-performance PAN/dual check valves with a little chance of breakdown used
-
Control Air Filter
A control-purpose compressed air filter installed to prevent valves and pneumatic solenoid valves from malfunctioning
-
Minimization of Purge Air Loss
Minimizes compressed air loss through accurately calculated orifice caliber and precision processing
-
SAFETY VALVE
Ensures safety with KOSHA-certified safety valves
-
High-quality Desiccant
Stable dew points with high-quality active alumina including FRANCE AXENS
-
High-quality Pressure & Temperature Gauges
High performances and low faults with highly reliable pressure and temperature gauges
-
PLC and Touchpanel
A touchpanel designed for PLC and user convenience applied; able to operate and get diverse information easily
-
Electric Heater
An immersion heater with very low heat loss and great heating performances used
-
High-quality Ring Blower
Low noise and law faults despite long operation with a high-quality ring blower
-
High-quality Muffler
Minimizes noise from the purge with an Allied Witan’s muffler
-
Highly Reliable Auto Valve
Proven angle sheet and butterfly valves used
-
PARKER Pneumatic Solenoid Valve
Able to check operating conditions easily, using PARKER’s LED pneumatic solenoid valve
-
Efficient Compressed Air Distribution System
A bottom distributor installed to prevent the bias flow of compressed air in a large adsorption tower and provide stable dew points
Technical Specification
Design Conditions
- Inlet Pressure : 7 barg
- Inlet Temperature : 38 ℃
- Dew Points : -40 ℃ @ ATM
- Design Temperature : 250 ℃
- Design Pressure : 9.7 barg
- Differential Pressure : 0.2 bar
References
- Those with - 40℃ or below dew points are also customizable.
- ASME specifications in addition to KS are also customizable.
- A unit with 9.8barg or higher operating pressure is custom-made.
- Special-purpose models in addition to the proposed specifications are also customizable.
- Large models biggerthan those stated in the specifications above are also customizable.
- The specifications are subjectto changes without notice for productimprovement.
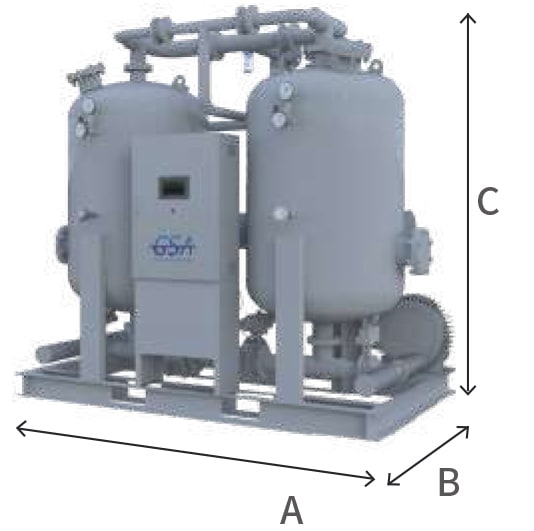
Model | Connection | Flow Rate | Heater | Blower | Power Supply | Dimensions (mm) | Desiccant Amount *N *Note 1 |
Weight *Note 2 |
|||
---|---|---|---|---|---|---|---|---|---|---|---|
A | N㎥/hr | kW | kW | V / Ph / Hz | A | B | C | kg/2Tower | kg | ||
P E H B |
150 | FLG. 40A | 250 | 3.4 | 1.5 | 380 / 3 / 60 | 970 | 1100 | 1890 | 110 | 500 |
200 | FLG. 40A | 370 | 4 | 1.75 | 970 | 1100 | 1990 | 170 | 650 | ||
285 | FLG. 40A | 495 | 4.5 | 1.75 | 1150 | 1200 | 2240 | 210 | 900 | ||
350 | FLG. 50A | 660 | 7.5 | 1.75 | 1150 | 1200 | 2540 | 280 | 1000 | ||
430 | FLG. 50A | 870 | 9 | 1.75 | 1150 | 1200 | 2570 | 390 | 1200 | ||
560 | FLG. 65A | 1050 | 10 | 3 | 1250 | 1300 | 2670 | 460 | 1500 | ||
720 | FLG. 65A | 1380 | 12 | 3 | 1450 | 1400 | 2700 | 520 | 1800 | ||
900 | FLG. 80A | 1680 | 15 | 3 | 1450 | 1400 | 2705 | 700 | 2000 | ||
1100 | FLG. 80A | 1950 | 18 | 6.3 | 1700 | 1600 | 2750 | 860 | 2400 | ||
1350 | FLG. 80A | 2280 | 20.4 | 6.3 | 1700 | 1700 | 2850 | 1000 | 2900 | ||
1550 | FLG. 100A | 2950 | 28.5 | 7.5 | 1900 | 1700 | 2950 | 1050 | 3400 | ||
2100 | FLG. 100A | 3700 | 33 | 9 | 2400 | 1800 | 2990 | 1560 | 4000 | ||
3000 | FLG. 150A | 5400 | 44 | 13 | 2500 | 1950 | 3250 | 2100 | 4800 | ||
4100 | FLG. 150A | 6600 | 56 | 15 | 3200 | 2300 | 3250 | 2900 | 6000 | ||
4500 | FLG. 150A | 7500 | 62 | 15 | 3200 | 2400 | 3250 | 3200 | 6500 | ||
5400 | FLG. 150A | 8500 | 70 | 20 | 3200 | 2500 | 3300 | 3780 | 7300 | ||
6000 | FLG. 200A | 10500 | 85 | 22 | 3400 | 2500 | 3430 | 4200 | 8100 | ||
7000 | FLG. 200A | 12000 | 100 | 27 | 3600 | 2500 | 3430 | 4900 | 10300 | ||
9000 | FLG. 250A | 15000 | 110 | 30 | 4000 | 3000 | 3430 | 6400 | 12300 |
Correction Factors
Correction Factor by Inlet Air Temperature | ||||||||||||
---|---|---|---|---|---|---|---|---|---|---|---|---|
Inlet Air Temperature (℃) | 25 | 30 | 38 | 45 | 50 | |||||||
Correction Factor | 1.12 | 1.05 | 1.00 | 0.7 | 0.55 | |||||||
Correction Factor by Inlet Air Pressure | ||||||||||||
Inlet Air Pressure (barg) | 4 | 5 | 6 | 7 | 8 | 9 | N/A | N/A | N/A | N/A | N/A | N/A |
Correction Factor | 0.6 | 0.72 | 0.87 | 1.00 | 1.1 | 1.15 | N/A | N/A | N/A | N/A | N/A | N/A |

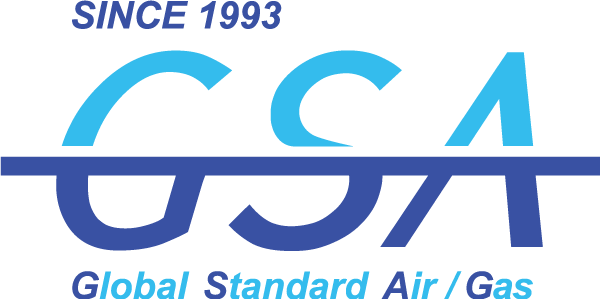
Desiccant Air Dryer
- +82 31-798-0171~3
- FAX : +82 31-798-0175