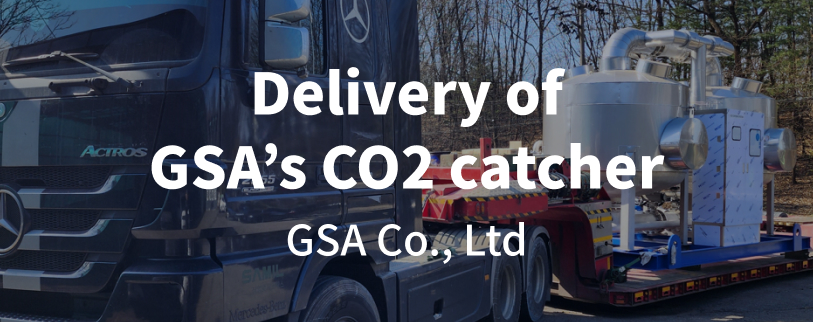
In addition to nitrogen and oxygen, the air we breathe contains small amounts of carbon dioxide (CO2). The concentration of CO2 in the air around us today is about 410 ppm. While compressing air with a compressor, no more CO2 is added, but it is also not removed.
Therefore, compressed air also contains a small amount of CO2. Like the air we breathe, CO2 is not harmful to most compressed air applications.
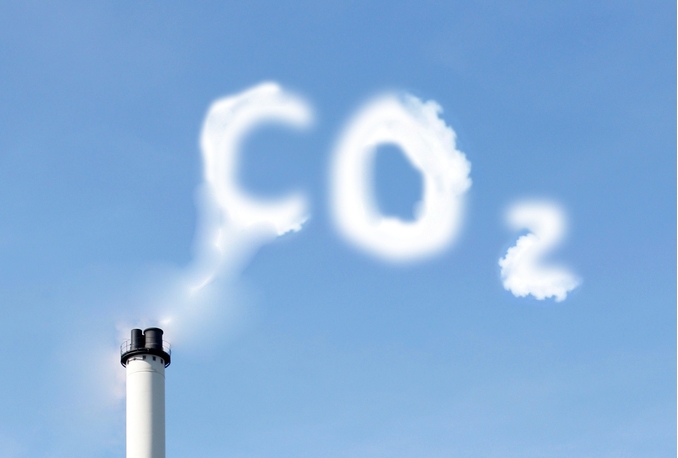
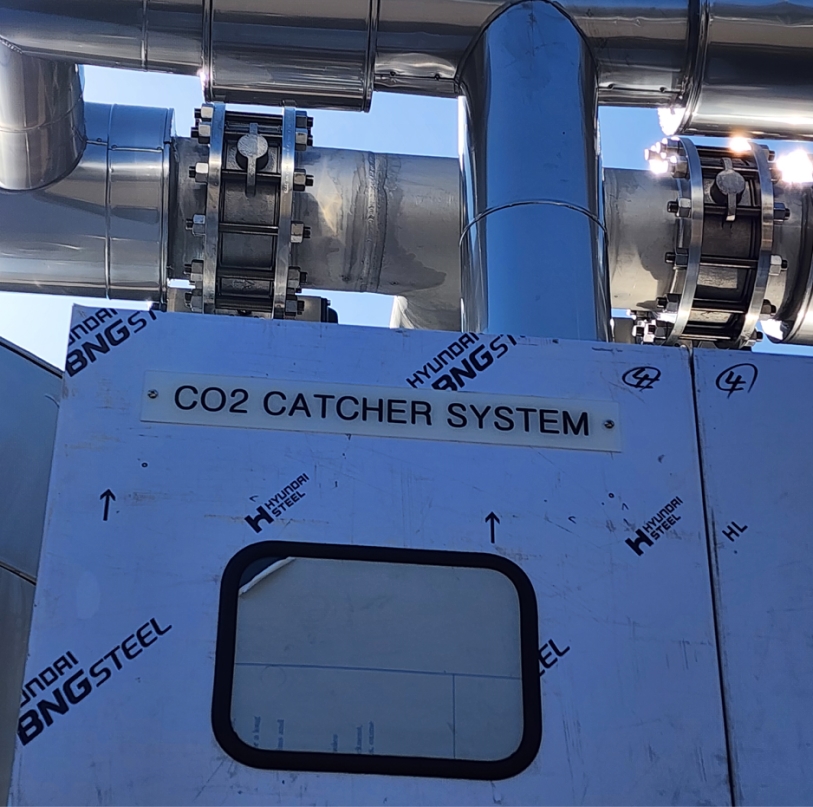
However, some applications require ultra-dry, CO2-free air.In these applications, if the CO2 contained in compressed air is used without being properly removed, it can cause serious problems with the quality of the final product.
For example, when CO2 comes into contact with the chemical raw materials used in lithium battery cells, it has a negative impact on their lifespan and quality.
The equipment used to remove CO2 is called a CO2 Catcher or CO2 Removal equipment, and GSA – Global Standard Air/Gas specializes in designing and producing this equipment.
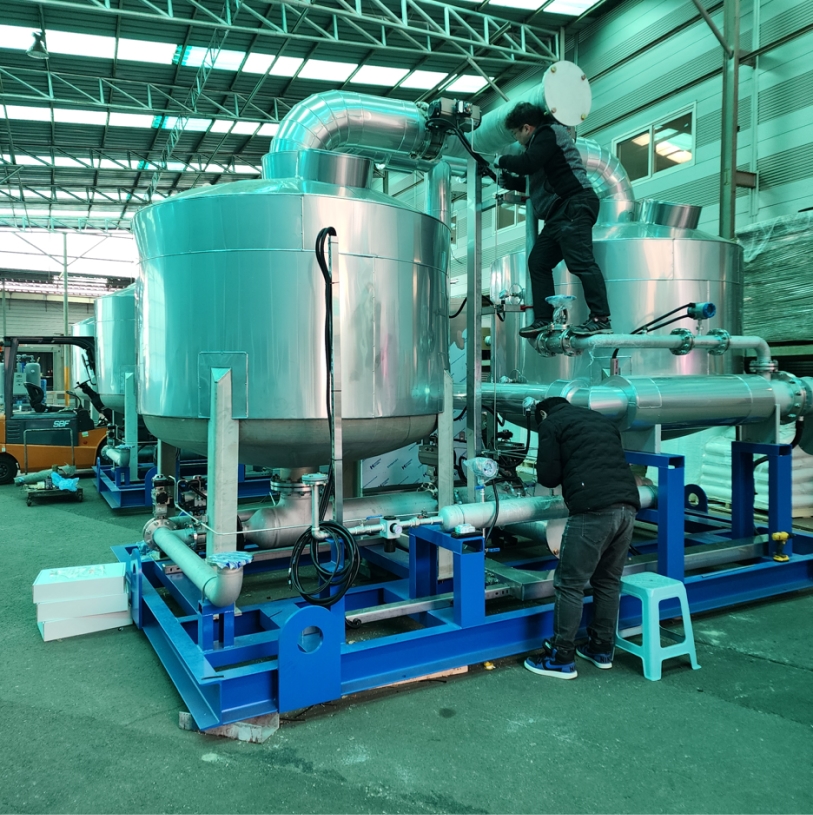
Today, I would like to introduce you to the delivery story of our CO2 catcher, delivered on April 1, 2024, with photos.
The equipment delivered this time is made of stainless steel, and has a total of 8 units, each with a capacity of 3,600Nm3/h inlet flow rate.
This is a project that is being carried out on a very tight schedule, with the delivery and test run of four units each to be completed twice in April and June 2024.
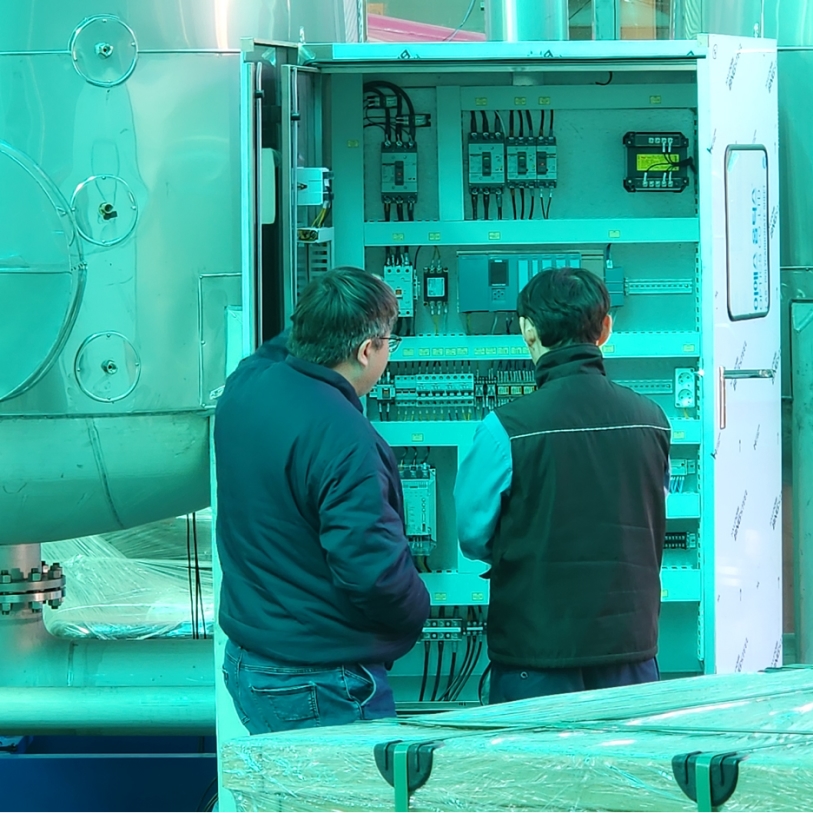
Our engineers are inspecting the inside of the PLC board that has been manufactured and tested once again before delivery.
The inlet flow rate of this CO2 catcher is 3,600Nm3/h and the inlet pressure is 0.4barg.
And CO2 outlet purity is less than 5 ppm.
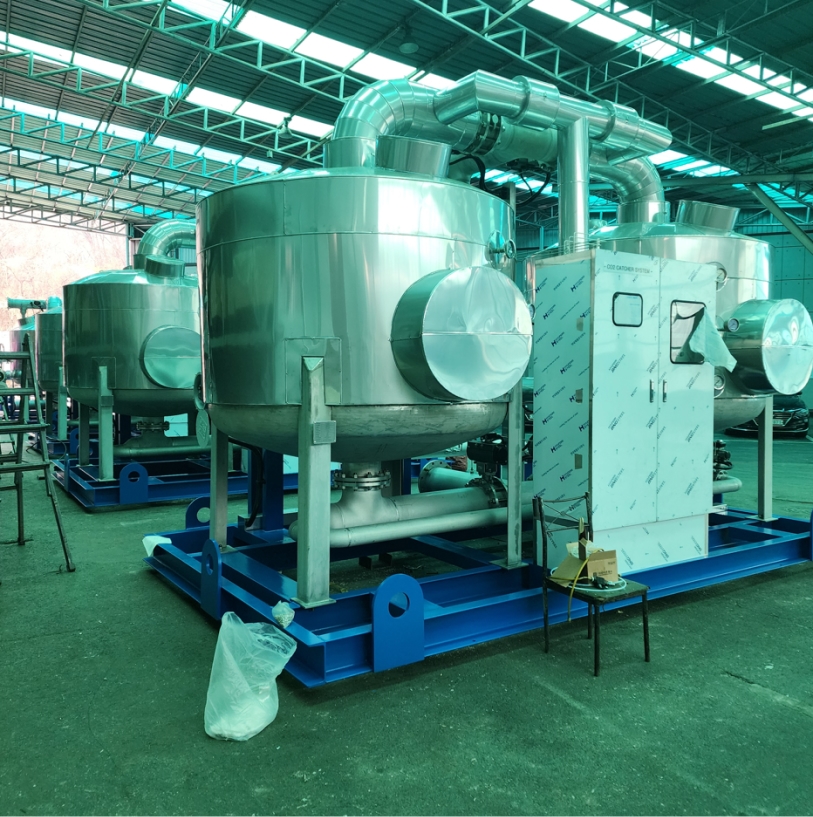
There are a total of 4 CO2 catchers being delivered this time, and 4 units are lined up in the company’s factory yard, waiting for delivery, which is one day away.
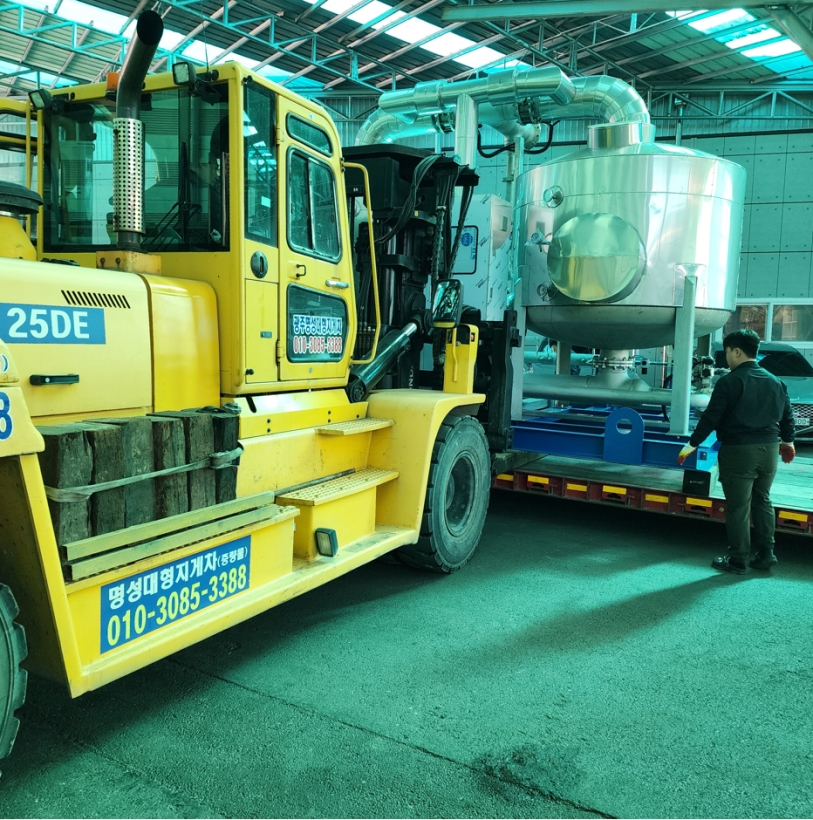
One CO2 catcher is a large and heavy equipment measuring 5000mm wide, 2800mm long, 2900mm high, and weighing 8,900kgs.
Therefore, since it was not possible to lift the device with an ordinary forklift, loading was carried out using a 25 ton forklift.
Even though the CO2 catcher is very large, it looks very compact when held on a forklift.
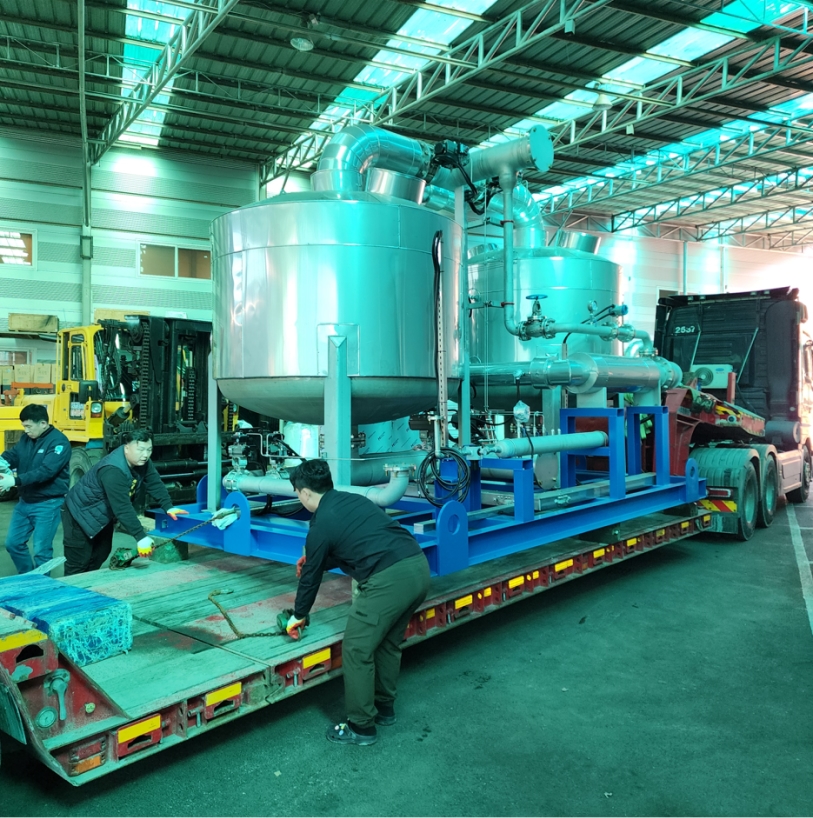
As the height of the equipment is 2900mm, there is a risk that it may not pass the overpass during road transport, so a low bed trailer was called for loading.
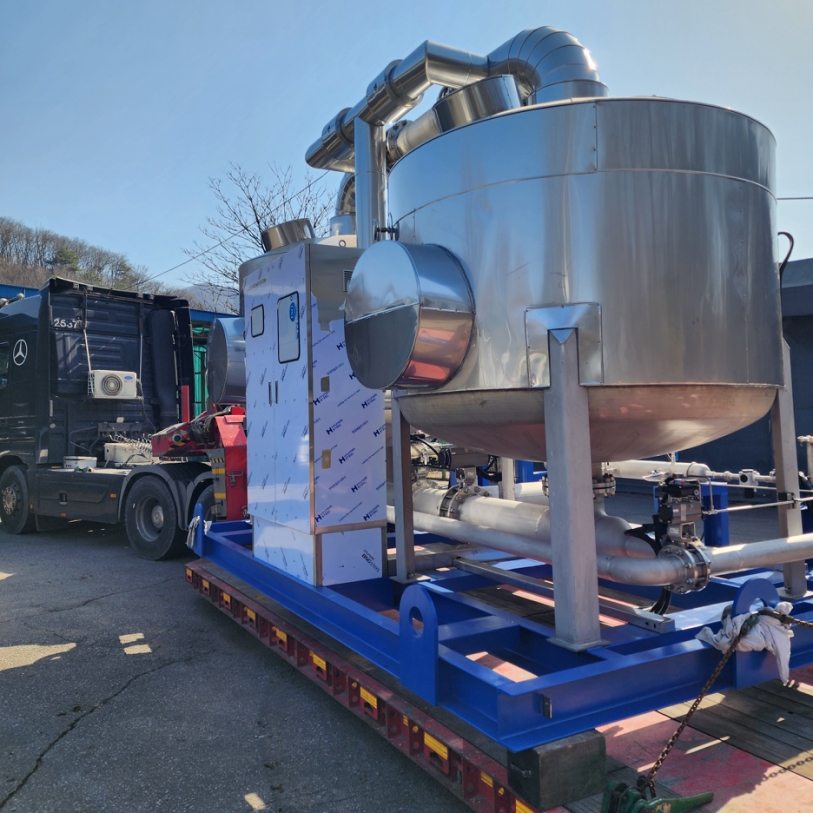
The principle is to package for transport, but since the weather was clear and the distance to the destination was less than 3 hours, after discussing with the buyer, it was decided not to package but to transport.
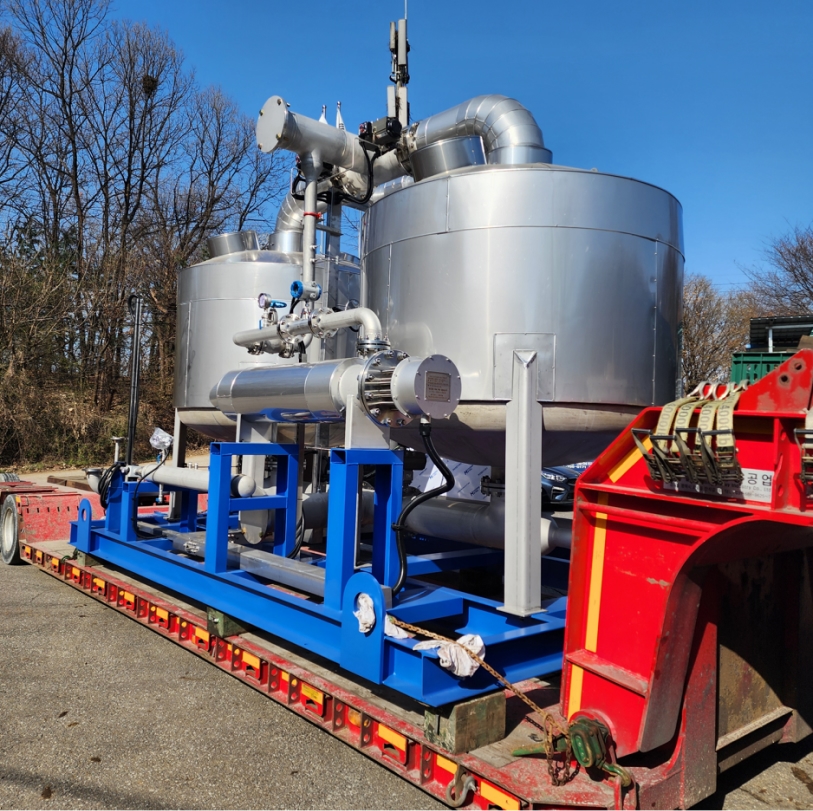
Because the equipment should not fall to the road during transportation, chains were used to secure the equipment.
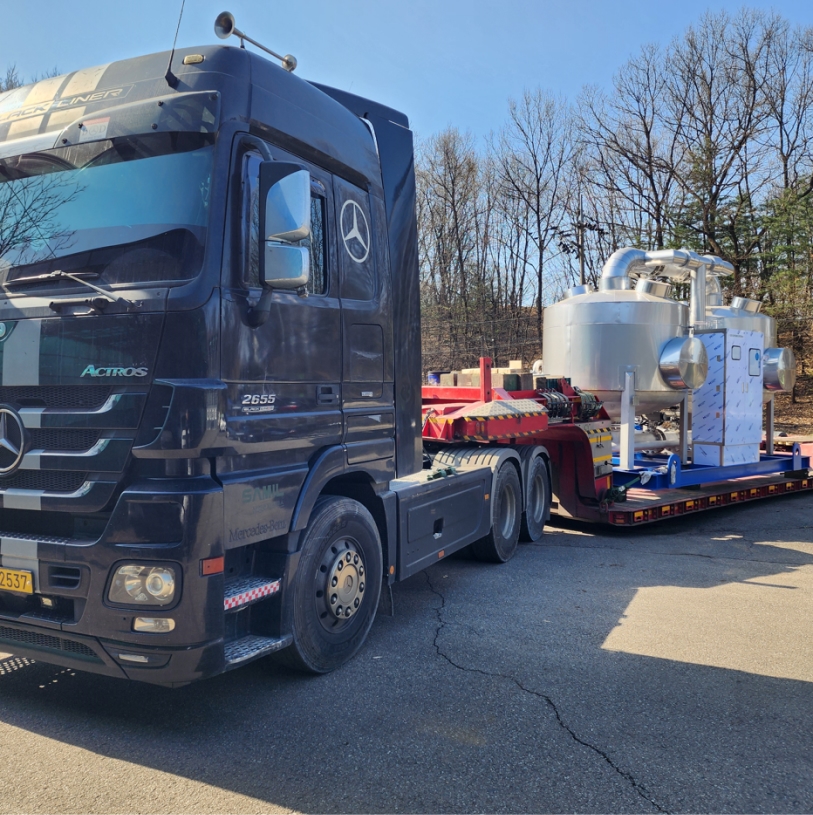
A trailer carrying equipment is slowly leaving the factory in reverse.
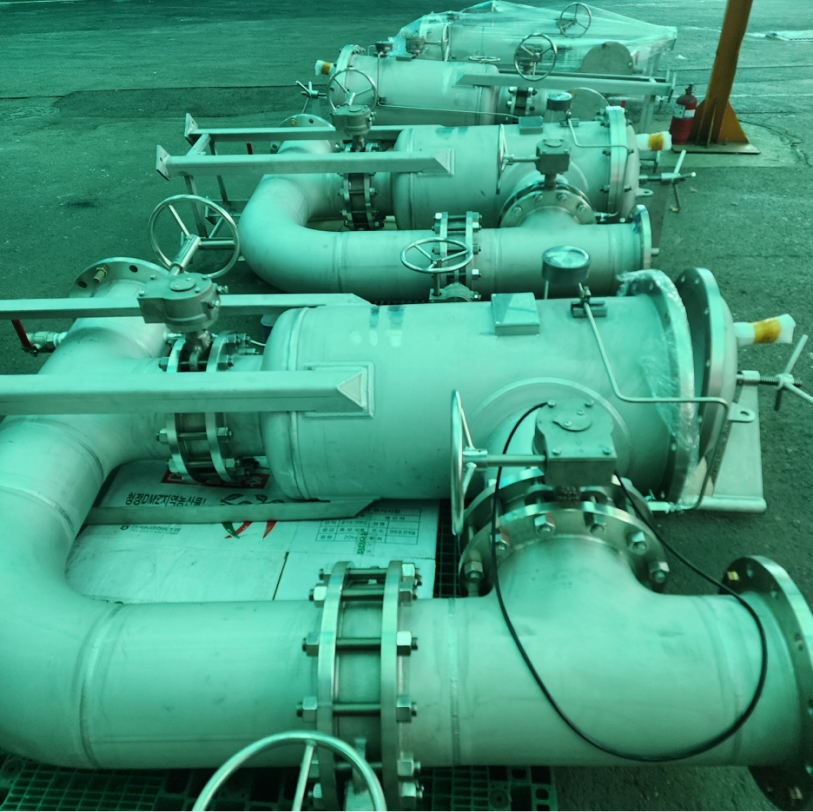
The stainless steel low-pressure air filter delivered with the CO2 catcher has also been manufactured and is awaiting shipment.
The trailer carrying the equipment arrived safely at the installation site less than three hours after leaving the GSA factory.
Since the site where the first four CO2 catchers delivered was installed on the second floor of the building, a crane and special lifting equipment were used to raise the CO2 catchers one by one to the second floor.
The angle of the crane was turned to 90 degrees to allow the CO2 catcher to enter the entrance to the second floor of the building.
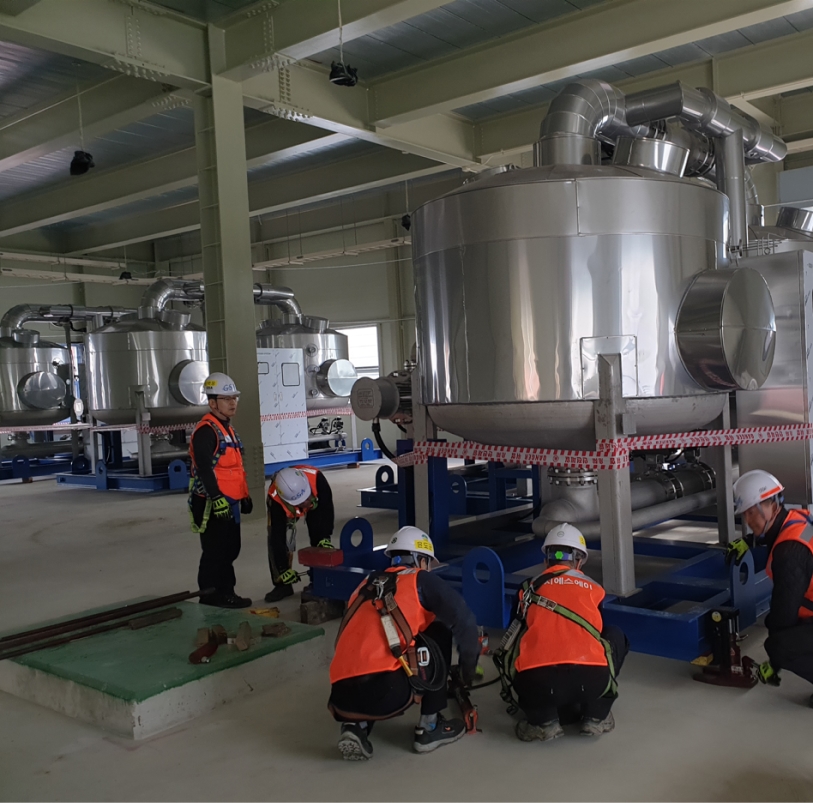
All four CO2 catchers delivered in the first round were safely moved to the second floor of the factory where installation will take place.
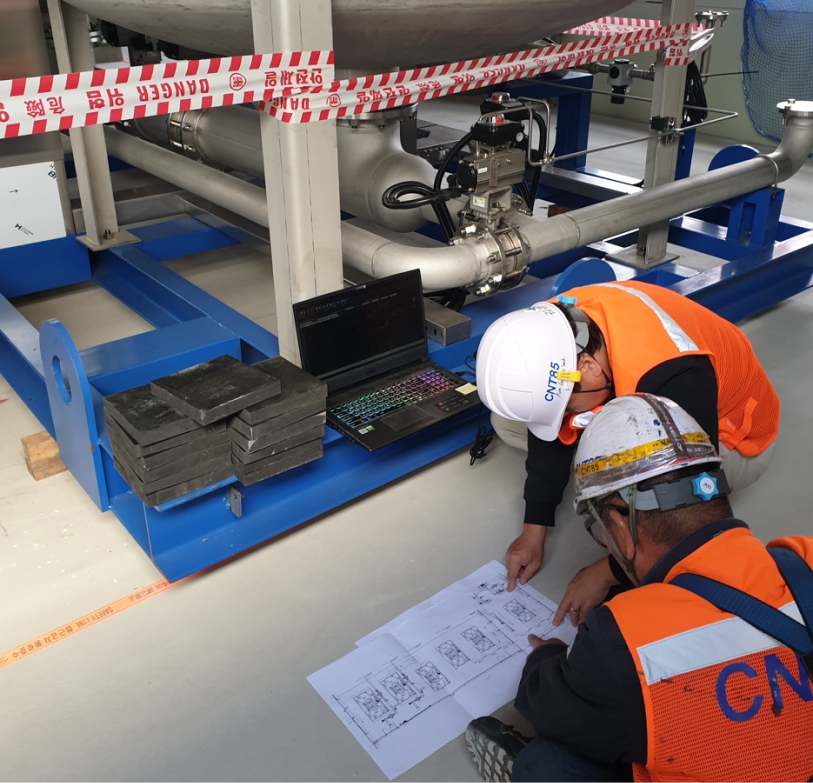
Workers are checking the drawing where the CO2 catcher will be installed.
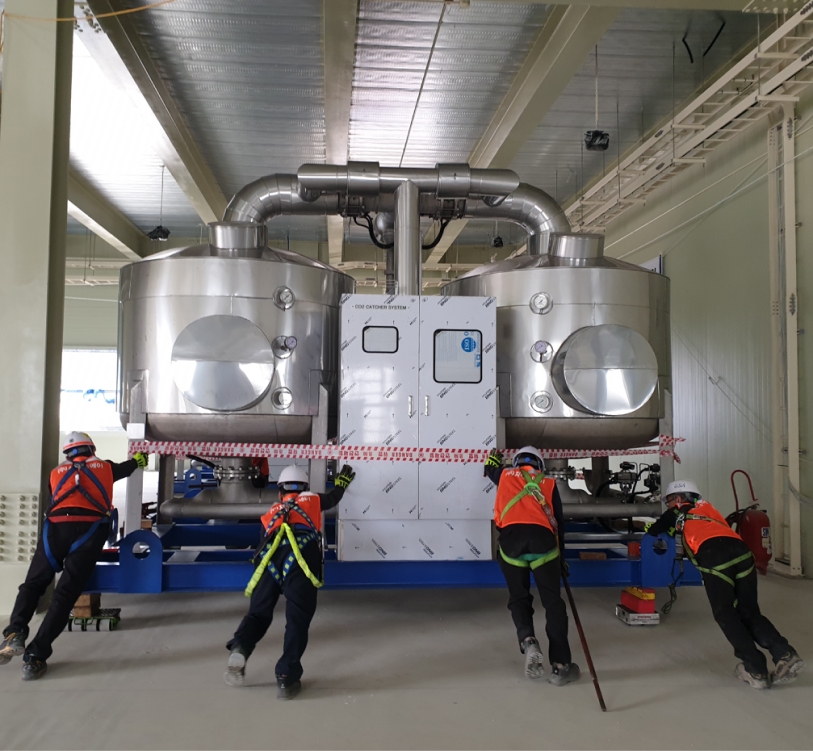
Several roller were inserted into the bottom of the CO2 catcher, and four workers are pushing it together to move it to the location where the device will be installed.
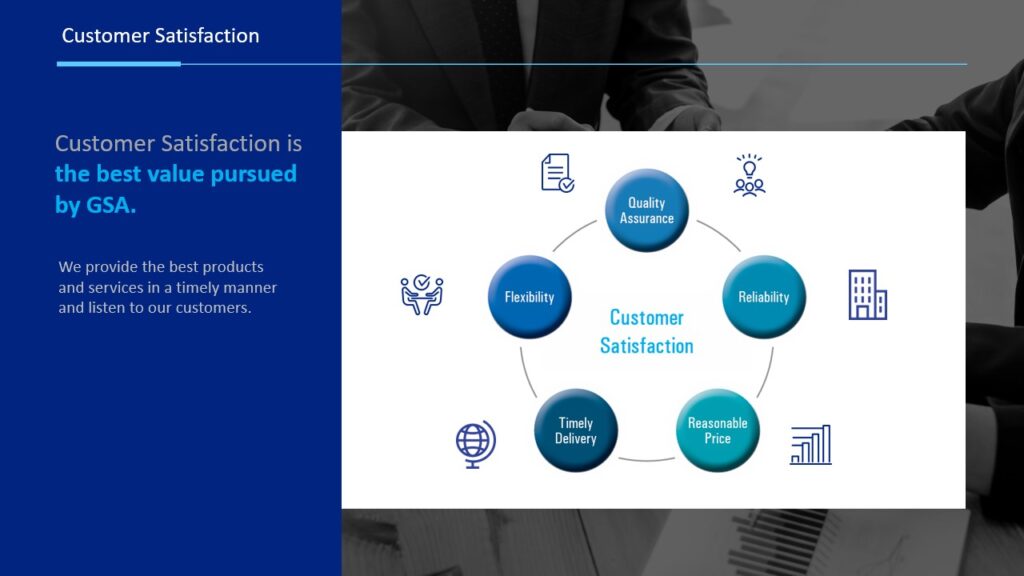
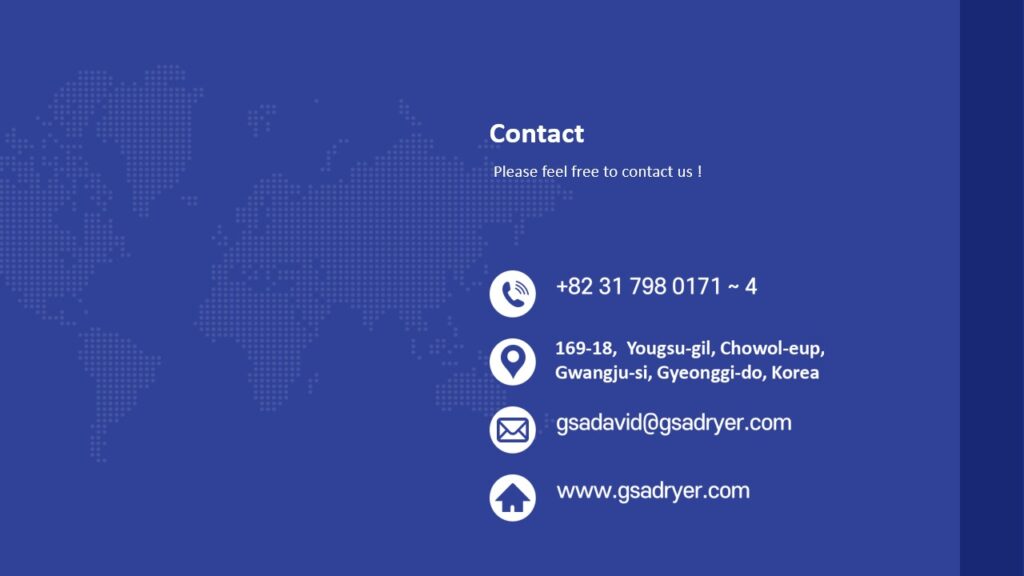
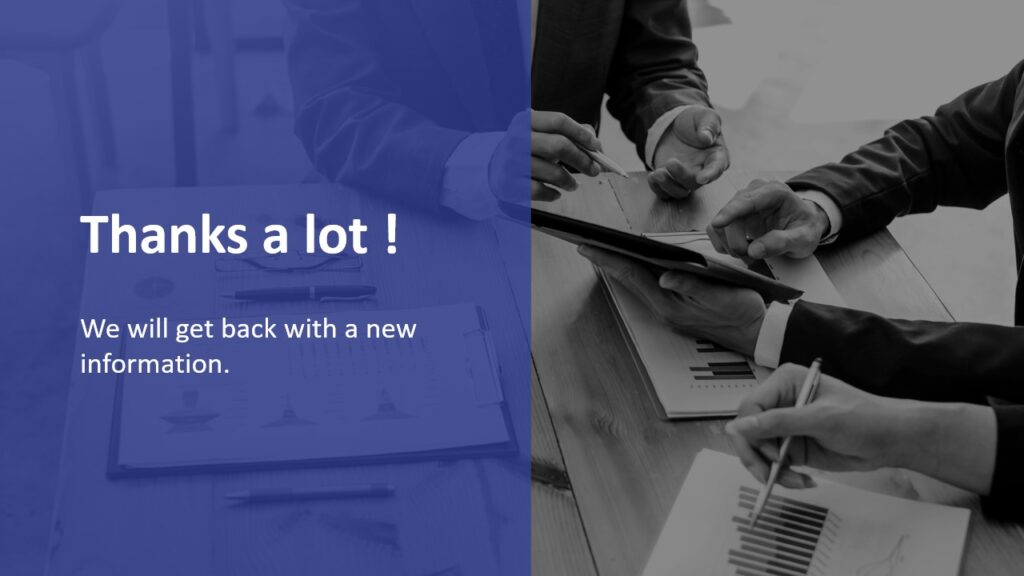