GSA's compressed air treating equipment turning Top air quality
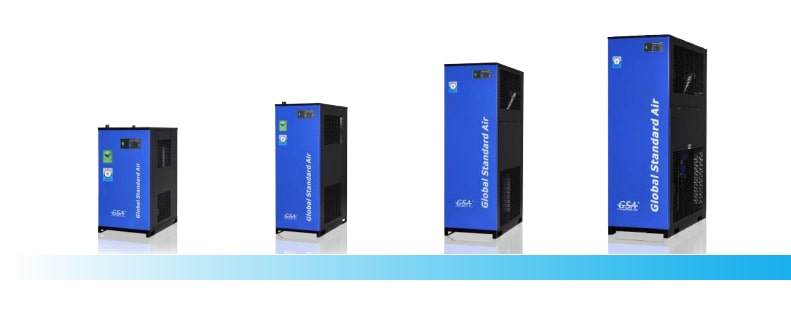
Energy saving by generation-II refrigerated air dryer
Generation-II, Energy-saving, Refrigerated Air Dryer
GSA’s generation-II, energy-saving refrigerated air dryer is a cycling system designed to save energy in a simple and efficient fashion. It is relatively simple, compact and highly reliable compared to products which use variable-speed drive (VSD) designed to control the RPM of the refrigerant compressor and a brushless DC (BLDC) motor or those with phase change materials (PCM) or thermal mass.
The aluminum heat exchanger of the generation-II, energy-saving refrigerated air dryer plays a role of thermal mass which has great heat transfer performances. Since the product is made with a single material, it has no thermal resistance. Therefore, cooling energy stored in the heat exchanger can be utilized efficiently. It generates the greatest efficiency at the lowest costs when load is low or the compressed air use pattern is intermittent with a long length of time by maximizing the use of cooling energy accumulated in the heat exchanger.
Stored Heat of Aluminum Heat Exchanger
Compared to other heat exchangers, an aluminum heat exchanger is greater in terms of accumulated heat under the same mass due to high specific heat. With greatthermal conductivity, it displays great cooling effects of compressed air with high and stable dew points. Under same mass, the machine is 2.3 times and 1.9 times greater than copper and stainless steel respectively in terms of cooling capacity. With great thermal conductivity, furthermore, it ensures stable operation according to load changes.
Heat Exchanger | Materia | Specific Heat (J/kg) | Thermal Conductivity (kcal/mh℃) |
TherHeat Capacity (Based on 1kg x △10℃) |
Ratio of Heat Storage Capacity |
---|---|---|---|---|---|
Shell & Tube | Copper | 389 | 332 | 3890 | 100% |
Plate heat exchanger | Stainless | 464 | 14 | 4640 | 120% |
Aluminum Block | Aluminum | 896 | 196 | 8960 | 230% |
Comparison of Operating Costs for Decade
Highly reliable generation-II, energy-saving dryer
Features of the machine built with diverse innovative technologies

High-efficiency Aluminum Heat Exchanger
With a high-efficiency aluminum heat exchanger, GSA refrigerated air dryer offer larger heat-exchange area and performance guarantees of stable dew point than any other brands adopting other types of heat exchangers such as shell & tube and plate ones. Made with a single material, it has no thermal resistance and a little risk of corrosion or freezing burst.
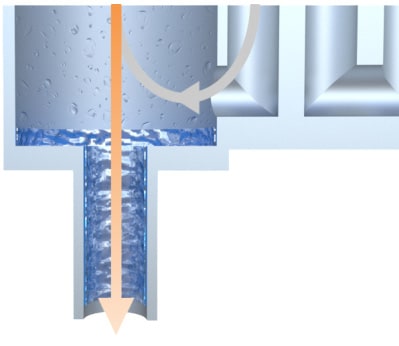
Efficient Condensate Separation Technology
It separates a large amount of condensate produced during heat exchange efficiently by increasing the volume of a separator. Therefore, this machine offers stable performances and dew points even under diverse load and pressure conditions.

Minimizing the loss of compressed air with low differential pressure
The occurrence of differential pressure was minimized by offing a large heat-exchange area and a sufficient cross-sectional area for compressed air flow. The efficiency of the compressed air system can be enhanced due to low differential pressure after increasing heat-exchange efficiency and minimizing resistance. In addition, operating costs can be reduced.
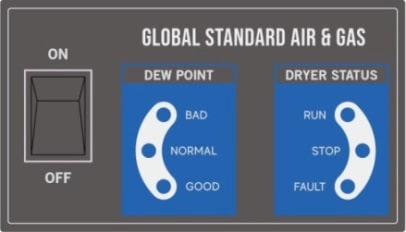
Simple and Smart Controller
The simple but functional controller helps users observe the exact dew point and check energy-saving status through the ECO lamp. In addition, this multifunctional controller offers a 4.3” color TFT touch panel (optional) and various mobile communication features such as WiFi and BT.

Highly reliable drain without loss of compressed air
The efficiency of compressed air facilities was enhanced by applying a magnetic float-integrated AUTO DRAIN which guarantees no loss of compressed air. The magnetic float ensures great operating performances. In addition, decrease in drain performances or failure resulting from oil or diverse substances in the air was minimized.
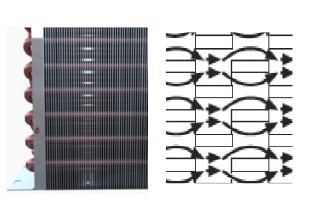
Efficiency maximization with the use of a high-efficiency condenser
To ensure stable performances at high temperature or under unfavorable circumstances, grooved copper tube and corrugated split fin were applied. In addition, a condenser which has a high coefficient of heat transfer due to great fin adhesion after complete and uniform tube expansion was adopted. Therefore, it ensures stable operation in diverse situations such as a high-temperature region.
Technical Specification Table
Design Conditions
- Inlet Pressure: 7 barg
- Inlet Temperature: 38℃
- Pressure Dew Point: 2-10℃
- Design Pressure: 14 barg
- Design Temperature: 70℃
- Ambient Temperature: 32℃
References
- All models use R-134a and R-22. We can also offer other alternative refrigerant specifications.
- The flow rate is set at 60Hz.
- It can be custom-ordered if electrical specifications are different.
- It can be custom-made if operating pressure is 15barg or higher.
- Large models above the specifications can also be provided.
- Specifications are subject to changes without notice for quality improvement.

Model No. | Connection Size |
Air Compressor Applied |
Flow Rate | Minimum Electric Energy |
Power Specifications |
Dimensions | Weight | |||
---|---|---|---|---|---|---|---|---|---|---|
A | HP | N㎥/min | kW | V / Ph / Hz | A | B | C | kg | ||
H Y D |
5N2 | PT 15A | 5 | 0.5 | 0.3 | 220 / 1 / 50, 60 | 247 | 557 | 723 | 36 |
7N2 | PT 15A | 7 | 0.8 | 0.31 | 247 | 557 | 723 | 36 | ||
10N2 | PT 20A | 10 | 1 | 0.32 | 247 | 557 | 723 | 36 | ||
15N2 | PT 25A | 15 | 1.5 | 0.48 | 428 | 508 | 709 | 45 | ||
20N2 | PT 25A | 20 | 2.6 | 0.56 | 428 | 508 | 709 | 45 | ||
30N2 | PT 25A | 30 | 3.9 | 0.9 | 358 | 658 | 864 | 66 | ||
50N2 | PT 40A | 50 | 6.7 | 1.4 | 408 | 708 | 952 | 89 | ||
75N2 | PT 50A | 75 | 10.5 | 2.1 | 458 | 798 | 1045 | 120 | ||
100N2 | PT 50A | 100 | 14.2 | 2.3 | 380 / 3 / 50,60 |
458 | 858 | 1145 | 126 | |
150N2 | PT 65A | 150 | 21 | 2.9(2.5) | 565 | 1005 | 1330 | 172 | ||
200N2 | FLG. 80A | 200 | 30 | 4.18(3.78) | 550 | 1200 | 1447 | 240 | ||
250N2 | FLG. 100A | 250 | 39 | 4.4(4) | 700 | 1200 | 1580 | 260 | ||
300N2 | FLG. 100A | 300 | 47 | 4.6(4.2) | 700 | 1200 | 1580 | 270 | ||
400N2 | FLG. 100A | 400 | 56 | 9.7(8.9) | 900 | 1591 | 1915 | 600 |
Capacity Correction Factor
Correction Factor by Inlet Air Temperature | ||||||||||||
---|---|---|---|---|---|---|---|---|---|---|---|---|
Inlet Air Temperature (℃) | 28 | 33 | 38 | 43 | 48 | 53 | 58 | 63 | 68 | 70 | N/A | N/A |
Correction Factor | 1.46 | 1.20 | 1.00 | 0.85 | 0.73 | 0.63 | 0.55 | 0.48 | 0.42 | 0.40 | N/A | N/A |
Correction Factor by Inlet Air Pressure | ||||||||||||
Inlet Air Pressure (barg) | 4 | 5 | 6 | 7 | 8 | 9 | 10 | 11 | 12 | 13 | 14 | 15 |
Correction Factor | 0.84 | 0.90 | 0.95 | 1.00 | 1.03 | 1.06 | 1.09 | 1.11 | 1.13 | 1.15 | 1.17 | 1.18 |
Correction Factor by Ambient Temperature (Air-cooled Machine) | ||||||||||||
Ambient Temperature (℃) | 27 | 32 | 37 | 40 | 45 | 50 | N/A | N/A | N/A | N/A | N/A | N/A |
Correction Factor | 1.05 | 1.00 | 0.92 | 0.82 | 0.76 | 0.69 | N/A | N/A | N/A | N/A | N/A |

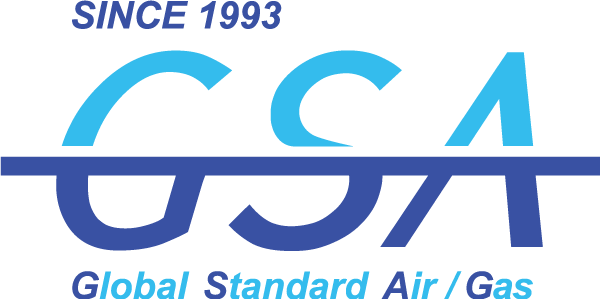
Refrigerated Air Dryers
- +82 31-798-0171~3
- FAX : +82 31-798-0175